Salons are places where people meet to socialize, talk and read. They can also be places where musicians perform.
Former staffers almost uniformly say that Jeffers focused on building traffic and paid too little attention to the editorial side of things. Contact I AM Salon now!
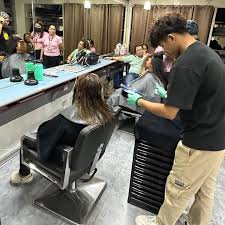
Many are worried that if Salon doesn’t make big changes soon, it could disappear forever.
Hairdressing
Hairdressing is the act of washing, cutting or styling a person’s hair, whether it be to give them a new look, make their hair healthier or for an occasion. This service can be provided in a salon, barbershop or other similar establishments. It is usually performed by a hairdresser, who has received training and certifications in their field.
A hairdresser may also recommend hair care products, such as shampoos, conditioners, and styling gels or waxes, to help clients maintain their styles between appointments. They may also provide scalp treatments and basic nail services, such as manicures and pedicures. Hairdressers must maintain cleanliness and sanitization standards in their work areas and follow all health and safety protocols.
Some salons hire salaried hairdressers who work set hours while others employ independent stylists who pay booth rent and work on a freelance basis. Hairdressers typically need to posses a cosmetology license in order to practice their craft. They should also have specialized knowledge of haircuts, dyeing and other chemical services. They should be able to offer consultations to clients in order to assess their needs and provide recommendations.
Hair salons are a place where people go to feel beautiful and pampered. They are a great place to escape from the everyday world and enjoy some time away from the stress of work and other commitments. Besides offering a variety of hair styling and coloring services, these salons usually have other amenities that can make their customers feel comfortable, such as spas and massages. In addition to that, many of these places also sell a wide range of hair products to help their customers maintain their style between visits.
In New York, you can find a number of great hair salons that cater to the city’s discerning clientele. These locations are known for their creative cuts, dynamic colors, and high customer satisfaction. They have everything you need to get a gorgeous, new look. Plus, the staff at these salons is always up to date on the latest trends and styles, so you can rest assured that you’ll be getting the best possible look for your new hairstyle.
Manicure
A manicure is a cosmetic treatment for the fingernails and hands that may be performed at home or in a nail salon. It includes trimming and shaping the nails, cleaning the cuticles (with a cuticle pusher or clippers) and removing dead skin cells, treatments with various liquids, massage of the hand, and application of nail polish. If the same treatment is done on the toenails, it is called a pedicure.
Manicures can range from basic to luxurious. They can be very relaxing, and they also make your hands look good. They are very effective in removing the top layer of dead skin, promoting new cell growth, and improving the overall appearance of your nails. Getting regular manicures and pedicures can also help to keep your nails strong and healthy.
During a manicure, your hands are soaked in warm water and soapy liquid to soften the cuticles. Then, the dead cuticle tissue is removed using a sterile manicure tool. Next, the nail is cleaned and trimmed, and then the nails are filed into a shape. Finally, a moisturizing cream is applied and massaged into the hands to complete the treatment.
Some manicures include nail art, which can be painted with acrylic or gel nails. These are often more durable than traditional paints, but they can be difficult to remove. They can also damage your natural nails, so it is best to limit them to occasional use.
Another type of manicure is a paraffin wax treatment. This involves covering the hands or feet in melted paraffin wax, which is then heated to a high temperature and infused with emollients and essential oils. The wax helps to moisturize and soften the skin and nails, and it also stimulates blood circulation. It can be very relaxing, and it is a great treatment for people who suffer from arthritis or other conditions that cause pain in the joints of the hands.
There are many different types of manicures and pedicures available, so it is important to find one that works for you. A professional nail technician will be able to advise you on what options will suit your needs.
Massage
Massage is an ancient healing art that stretches back to the beginning of time. It is an art that encompasses many techniques, each designed to affect different aspects of the body and mind. It is often used to reduce stress and relieve muscle pain. Whether it is a light touch to ease tension or deep tissue massage to relieve a knot, the benefits are numerous. It is a relaxing experience that stimulates the circulatory and lymphatic systems and helps with detoxification.
It increases the level of serotonin in the brain, which is thought to improve mood and feelings of well-being. It also triggers the relaxation response in your body, which decreases heart rate and blood pressure, and slows the release of stress hormones. It may be beneficial for individuals suffering from depression, insomnia, digestive problems, fibromyalgia, anxiety, and high blood pressure.
A professional massage therapist is trained to know how to identify your trouble spots and target them. They will start with gentle strokes and gradually build up the pressure to release your knots. If you are comfortable with it, you can communicate with them about the pressure and intensity of the massage. It is important to let them know if you have any specific preferences or are allergic to anything.
Some salons have specific focuses, such as aromatherapy, reflexology, or shiatsu. These massage techniques use oils to soothe the muscles and promote relaxation. They may also be used to relieve pain and promote general wellness. The massage therapist might also apply hot stones to increase the blood flow and provide a soothing sensation.
A therapist may also use effleurage, a technique that uses soft, light strokes to help the client relax and feel more comfortable. It is important not to press too hard on any bony prominences, as this can cause discomfort and be painful for the client. It is also a good idea to avoid massaging the belly button, as this can cause discomfort for some clients. In addition, a therapist should not massage any areas that are bruised or swollen.
Makeup
A makeup artist’s portfolio is a vital tool for their career, as it displays their skills and style to potential clients. It showcases a range of looks that can be used for a variety of occasions, including weddings, photo shoots, and fashion shows. The makeup artist’s website or social media accounts can be used to promote the portfolio and help increase bookings.
A great way to build a makeup portfolio is by photographing each look with professional lighting and using a variety of angles. It is also important to include a clear description of the look, along with any products and tools used. It is a good idea to include both before-and-after photos of each makeup look, as these can be more effective in conveying the artist’s skill and expertise.
In addition to providing a means for artists to share their work, a well-curated portfolio also builds credibility and professionalism. A reputable makeup artist has a strong understanding of their own style and aesthetic, which they use to create a unique identity in the industry. This helps them stand out from the competition and attracts a higher-quality clientele.
During the 17th and 18th centuries, salons were places where members of society could gather to socialize and discuss intellectual and artistic topics. These gatherings were popular among the aristocracy, and they also encouraged social mixing between women and men. The salons of the time also featured poets and writers, and were often supported by wealthy patrons.
The salon’s role in French culture has been analyzed by a number of scholars, including feminist, Marxist, and cultural historians. They have varying theories about its significance and impact, but all agree that it was an important social and cultural space for women. In the 1920s, Gertrude Stein’s salons, described in Ernest Hemingway’s novel A Moveable Feast and depicted fictionally in Woody Allen’s Midnight in Paris, became famous for their eclectic mix of guests, which included Pablo Picasso.
In addition to working in salons, makeup artists may also work on location, traveling to clients’ homes or event venues to provide services. This type of work can be fast-paced and high-pressure, and it requires flexibility and adaptability to meet the needs of each client.